大型複雜金屬零件3D打(dǎ)印技術及(jí)研究進展
點擊量:1388 發布時間:2017-03-10 作者:狀(zhuàng)邁(上海)增材製造技術有限公司
引言
大型複雜整體關鍵零部(bù)件的用量大小已經成為衡量(liàng)航空、航天等重大裝備技術先進性的(de)重要標誌,具有廣(guǎng)闊的應用(yòng)和發展前景。采(cǎi)用傳統鍛造、鑄造、焊(hàn)接等方法製備大型(xíng)複雜結(jié)構件,存在工序(xù)長、工藝複雜,對製造(zào)裝備的要求高以及成形技術難度大等諸多不足。鍛造方法製備大型複雜構件,不僅需要萬噸級(jí)以上的重型液壓(yā)工業裝備、大尺寸鍛造(zào)坯料的加工以(yǐ)及大尺寸鍛造模具製造,而且其製備零件的加工去除(chú)量大、機(jī)械加(jiā)工時(shí)間長、材料利用率低、生產周期長、製造成本高(gāo)。鑄造(zào)方法製備大型複雜構件,不僅需要(yào)重型或超重型鑄造工業基礎設施,而且采用鑄造加工的金屬結構件的性能往往不能滿足要求。焊接方法製備大型複雜構件,會導致焊(hàn)接區成(chéng)為整體構件的薄弱環節(jiē),從而降低構件的整體性能。3D打印技術可以製造飛(fēi)機、導彈、衛星等航空(kōng)航(háng)天(tiān)裝備(bèi)所需的高(gāo)溫合(hé)金、鈦合金及高強度鋼等(děng)大型複雜金屬構件。麵對傳統(tǒng)加工方法(fǎ)難以製備高性能大型複雜構件的難題,3D打印成形是目前的(de)唯一(yī)技術途徑。
1 金(jīn)屬3D打印技術原理與優勢
3D打印技術是一種采用高能束為熱源,通過(guò)材料逐層堆積,實現構件無(wú)模成形的數字化製造技術。金屬零件3D打印(yìn)技(jì)術原理是將金屬粉末或絲(sī)材(cái),在(zài)激光或電子束等(děng)加熱條(tiáo)件下,按軟件設定的路徑同(tóng)步熔化、堆積,最終成形出設計的零件實體。不同種類的金屬3D打印技術主要是通過(guò)熱源種(zhǒng)類、原材料狀(zhuàng)態以及成形方(fāng)式加以區分。金屬3D打(dǎ)印的(de)熱源主有激光、電子束(shù)和電弧,原材料狀態主要為(wéi)粉末和絲(sī)材,成形(xíng)方式主要包括鋪料、送料條件下的燒結成形及熔化成形。目前,廣泛用於金屬零件3D打印製造的(de)主要工藝有4種:激光直接熔化沉積成形(xíng)(laser direct melting deposition,LDMD)、激光選區熔化成形(selective laser melting,SLM)、電子束熔絲沉積成形(electron beam freeform fabrication,EBF)、電子束選(xuǎn)區熔化成形(selective electron beam melting,SEBM)。采用(yòng)3D打印技術製備金屬零件(jiàn),與傳統製造技術(shù)相比,具有以下(xià)突(tū)出優點:
1) 無(wú)需大尺寸毛坯製備和模具加工,無需大型或超大型工業裝備;
2) 零件具有快速凝固組織的晶粒細小、組織致密、成分均勻(yún)的特征,綜合力學性能優異;
3) 實現無模具近終成形,極大地節省材(cái)料,製造成本低、周期(qī)短;
4) 適用材料廣泛,可以製備(bèi)采用傳統方法難以加工的金屬材料(liào)。
5) 能夠在製造過程中根據零件的實際使用需要設(shè)計不同部位的(de)成分和組織(zhī),提高零件的綜合性能,擴大應用範圍;
6) 具有對構件設計的高度柔性與快速反應能力,降低新產品開發風險。
2 大型複雜金(jīn)屬零件3D打印研究進展
undefined
2.1 國外的研(yán)究進展
20世紀80年代末(mò),Sandia國家實驗(yàn)室(shì)、Los Alamos國家實驗室和Michigan大學得到美國能源部的資助,對(duì)激光直接製造技術(shù)(direct laser fabrication,DLF)展開了(le)研究;90年代中期,Sandia國家實驗室與(yǔ)UTC合作,開發了激光工(gōng)程化近淨成形技術(shù)(laser engineered net shaping,LENS),通過其開發(fā)的LENS技術,Sandia國(guó)家實驗室陸續開展了多種金屬材料的成形研究,主要包括(kuò)不鏽鋼、鈦合金(jīn)、高溫合金等(děng),期間成功製備了某衛星TC4鈦合金零件毛坯;1997年,Optomec Design公司獲得(dé)了LENS技術(shù)的(de)商(shāng)用化(huà)許可,推出了基於激光直接沉積(jī)技術的成套裝備,並為Sandia國家實驗室提供小批量的(de)零件製造,圖1所示為Optomec Design公司製備的鈦合金葉(yè)片;Los Alamos國家實驗室開展了鈦合金(jīn)、銅合金(jīn)、不鏽鋼(gāng)等多種金屬材料的(de)DLF技術研究,製備的零件性能與采用傳統加工方法(fǎ)製備的金屬零件性能相當(dāng);Michigan大學成立了(le)POM公(gōng)司,POM公(gōng)司主(zhǔ)要經營以金屬激光熔(róng)覆成(chéng)形(laser cladding fabrication,LCF)技術、直接金屬(shǔ)沉積(drect metal deposition,DMD)技術為基礎的大型金屬零件製造和維修裝(zhuāng)置,POM公司擁有與LENS技術相關的8項(xiàng)裝(zhuāng)置類專利技(jì)術,並通過其開發的成套(tào)裝備(bèi),製造了重達10 T的金屬零件。
1995年,在美國國防部高級研究計劃署和海(hǎi)軍研究所的資助下,Johns Hopkins大學、Pennsylvania大學和MTS公司合作開展了大(dà)尺寸鈦合金零件的柔性製造技術研(yán)究。基於前期的研究成果,MTS公司(sī)出資與Johns Hopkins大學、Pennsylvania大學合作成立了AeroMet公司。AeroMet公司獲得了美國軍方及3大美國(guó)軍(jun1)機製(zhì)造商Boeing、Lockheed Martin和Northrop Grumman公司的資助(zhù),開展了飛機機身鈦合(hé)金結構件(jiàn)的LDMD技術研究。2001年,AeroMet公司采用3D打印(yìn)技術(shù)為Boeing公(gōng)司艦載機試製了鈦合金(jīn)次承(chéng)力結構件,其中包(bāo)括尺寸為900 mm×300 mm×150 mm的航空翼根吊環,如圖2所示(shì),並於2002年(nián)實現了裝機應用。2002—2005年(nián)之間,AeroMet公司通過其(qí)Lasform工(gōng)藝係統製備了發動機艙推力梁、機翼轉動折疊接頭、內龍骨腹板、外掛架翼肋、發動機框(kuàng)等金(jīn)屬構件並實現裝機應用,其中大型(xíng)整體加強筋板鈦合金(jīn)發動機框尺寸達2 400 mm×225 mm×100 mm。
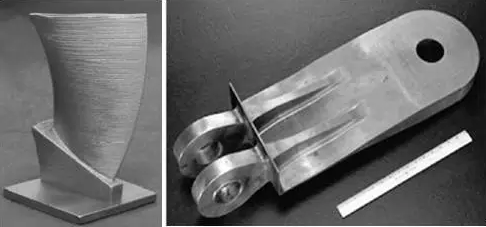
圖1 鈦(tài)合金葉片 圖2 F/A-18E/F翼根吊環
SLM研究方麵,20世紀90年代,德國(guó)Fraunhofer研究所提(tí)出采用(yòng)SLM製備金屬零件的方法,並於(yú)2002年研製成功。2013年,Fraunhofer研(yán)究所(suǒ)突破了鋁合金3D打印(yìn)的技術難題,並且由(yóu)EOS和Concept Laser等公司對其進行了推廣。目前,德國的EOS公司在(zài)SLM技術研發方麵處(chù)於世界領先(xiān)地位,其(qí)開發的EOSM400成(chéng)套裝備可以加工的金屬零件尺寸達400 mm×400 mm×400 mm。2012年,美國GE公(gōng)司采用SLM技術為LEAP噴氣(qì)式發(fā)動(dòng)機製造了燃油噴(pēn)嘴,並已接受了超過4 000台LEAP噴氣式發動機訂單。GE公司的激光3D打印發動機鈦合金構件最大尺(chǐ)寸達1 200 mm。圖3所示為GE公司製備的具(jù)有複雜內置流道結構的航(háng)空發動機葉片(piàn)。
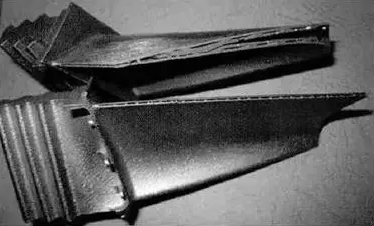
圖3 內(nèi)置流道的航空發動機葉片
EBF研究方麵,2002年,NASA的Langley研究(jiū)中心提出EBF,其合(hé)同商——美國Sciaky公(gōng)司,是當前EBF技術研究最領先的單位。在海軍、空軍、國防部(bù)等機構的支持下(xià),Sciaky公司聯合(hé)Boeing、Lockheed Martin公司開展了EBF研(yán)究,主要致力於大型航空金(jīn)屬零件的製造,製備的(de)鈦合金零件尺寸達5 800 mm×1 200mm×1 200 mm。目前,Sciaky公司成形鈦合金的最大速度可達18 kg/h,力學性能滿(mǎn)足AMS4999標準要(yào)求。圖4所示為Sciaky公司的大型航空鈦合金零件。
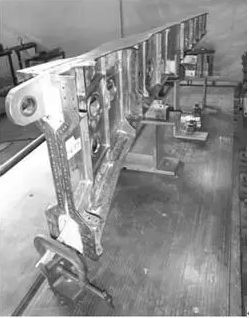
圖4 大型航空鈦合金零件
SEBM研(yán)究方麵,20世紀90年代,瑞典的Chalmers工業(yè)大學與Arcam公司合作開發出了SEBM技術。2003年,Arcam公司開發推出了首台商用的SEBM設備,並(bìng)相繼推出了一係列SEBM產品。目前(qián),Arcam公司的SEBM係統研究處於(yú)世界領先(xiān)地位,具有世界上最(zuì)大的(de)SEBM設備,有效加工範圍為(wéi) 350 m×380 mm。SEBM技術(shù)在航空航天領域的發展迅速(sù),多家單位都開展(zhǎn)了利用(yòng)SEBM技術製(zhì)造航空(kōng)發動機複雜零件的研究。例如,意(yì)大利AVIO公司利用SEBM技術製備出了TiAl基合金發動機葉片,引起了廣泛關注。
undefined
2.2 國(guó)內的研究進展
1997年,西北(běi)工業大學(xué)的“金屬粉材激光立體成形的熔凝組織與性能研究”獲得航空科學基金重點項目資助,是中國金屬3D打印第一個正式(shì)立項的(de)科研(yán)項目。近年來,西北工業大學采用激光3D打印技術為中國商飛公司製造了大(dà)飛機C919的中(zhōng)央翼肋TC4上(shàng)、下緣(yuán)條構件,尺寸為3 000 mm×350 mm×450 mm,質量196 kg,並(bìng)通過(guò)了中國商飛(fēi)公司的性能測(cè)試。采用激光3D打印技術,西北工業(yè)大學(xué)還製備了軸承(chéng)座後機匣、超音速飛行器方向舵、複雜內部結構零件等構件,圖5為航空發(fā)動(dòng)機(jī)軸承後(hòu)機匣。在國內LDMD研(yán)究領域中,北京航空航天大學是另一家處於領先水平的科研單位。2007年,北(běi)京航空航天大學(xué)突破了(le)飛機鈦(tài)合金大型、主承力結構件激光3D打(dǎ)印關鍵技(jì)術,研製(zhì)出世界(jiè)最大飛機鈦合金大型結構件激光快速成(chéng)形(xíng)工程化成套裝(zhuāng)備,成形室尺寸為4 000 mm×3 000 mm×2 000 mm。通過長期深入研究,北京航空航天大學研製了TA15、TC4、TC11等大型、複雜、整體、主承力飛機鈦合金加強(qiáng)框(kuàng)及A-100超高強度鋼飛機起落架等關鍵構件,並實現了(le)包括C919大型客(kè)機(jī)在內的多(duō)種型號飛機上的裝機應用,使我國成為世界上唯一突破飛(fēi)機鈦合金大型整體(tǐ)主承力構件激光3D打印技術並(bìng)實現裝機(jī)應用的國家。圖6所示為北京航空航天(tiān)大學(xué)研製的某型號飛機“眼鏡式”鈦合金大型、複雜、整(zhěng)體、主承力構件加強框。
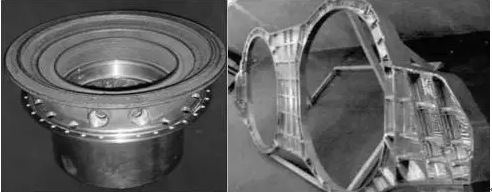
圖5 航空發動機零件 圖6 鈦合金主承力構件加強框
在SLM研(yán)究方麵,我國最早開展激光SLM技術研究的單位為華(huá)南理(lǐ)工(gōng)大(dà)學和華中科技(jì)大學。華南理工大學專注於SLM技術的醫學(xué)植入體應用,並開發出了國內第一套SLM設備DiMetal-240。華中科技大學則(zé)首先開拓了SLM技(jì)術的航天應用,開發擁有自主知(zhī)識產權的(de)SLM設備,並成形出尺寸達615mm×216 mm×236 mm的複雜結構樣件。此外,還有多家單位(wèi)開展了SLM研究並取得實際成(chéng)果(guǒ),如西安交(jiāo)通大學製造出高表麵質量和幾何尺寸精度的複雜空(kōng)心葉片樣件;中科(kē)院沈陽自動化研(yán)究所(suǒ)成(chéng)功製備出具有一定複雜外形,能滿足直接使(shǐ)用要求的金屬零(líng)件;沈陽航空航天大學激光快速成形實驗室開發出最大成形尺寸為200 mm×200 mm×100 mm,精度達0.1 mm的加工係(xì)統。
在EBF研究方(fāng)麵,中航工業北京航空製造(zào)工程研究所於2006年開(kāi)始EBF技術的研究工作,開發了(le)目前國內最大EBF設備,有效加工範圍為(wéi)3 000 mm×1 500 mm×800 mm,圖(tú)7所示為國產EBF設備及其製備的零件。利用其研(yán)製的EBF設備,中航工業北京(jīng)航空製造工程研究所開(kāi)展了TC4、TC11、TC21等鈦合金以及A-100超高強(qiáng)度鋼的EBF工藝研究(jiū),研製了大量鈦合金零件(jiàn)和試驗件,成形出尺寸為2 100 mm×450 mm×300 mm的(de)鈦合金大型、主承(chéng)力結構件,並於2012年率先實現了在國內飛機(jī)上的裝機應用。
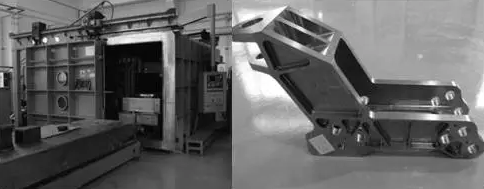
圖7 國產EBF設備及其製備的零件
SEBM研究方麵,清華大學先進成形製造教育部(bù)重點實驗室研製出國內第一台EBSM-150電子束快速成形係統,並與西北有色金(jīn)屬研究院聯合開發(fā)了第二(èr)代EBSM-250電子束快速成形係統。基於與清華大學合作開發(fā)的成套裝備,西北(běi)有色金屬研究院對鈦合金、TiAl合金(jīn)的SEBM成形工藝及變形控製等(děng)方麵進行了深入研究,申請了相關專利,並製造出了複雜的鈦合金葉輪葉片。
3 存在問題和研究方向
undefined
3.1 存在問題
1) 工(gōng)藝質量。
由於高(gāo)能束的長期(qī)周期性劇烈加熱和冷卻以及工藝參數、外部環境、掃描路徑的變(biàn)換等不連續和不穩定因素,導致大型複雜零件出現變形開裂、孔洞、夾雜、裂紋等問題。此外,3D打印金屬零(líng)件的疲勞強度、長期使用可靠性和質量的一致性難以得到保證,製造效率、質量和(hé)成本之間的關係(xì)難以協調。金屬零件3D打(dǎ)印技術還缺乏對材料問題以及材料與工藝(yì)的關係等基礎問題的研究,尚未找到材料、工藝和設備之間協調控製的方法。
2) 成形(xíng)裝(zhuāng)備(bèi)。
目(mù)前金(jīn)屬零件3D打印的能量(liàng)源主要為激光和電子束,激光、電(diàn)子束具有能量集中、加熱效率高、成(chéng)形材料廣泛的特(tè)點。然而,目前的激(jī)光、電子束技術自身並不(bú)是十分成(chéng)熟,且存在設備昂貴、複雜(zá)等缺點,增加了打印成本,限製了金屬零件(jiàn)3D打印(yìn)的普及。此外,大(dà)型複雜金屬零件3D打印需要解決更多的技術問(wèn)題,對成形裝備及其穩定性提出(chū)更高的要求(qiú),如(rú)高(gāo)匯聚光-粉耦合(hé)打印頭、大型(xíng)真空鋪粉係統以及大跨(kuà)度(dù)高精度數控工作台等。
3) 控製軟件。
分層(céng)處理、掃描路徑和策略在某種程度上決(jué)定了零(líng)件能否順利(lì)完成最終成形。大型複雜(zá)金屬零件3D打印(yìn)成形(xíng)過程中,分層處理、掃描路徑和策略顯得尤為重要,科學的路徑(jìng)規劃能(néng)夠(gòu)很大程度上減緩沉積材料的熱(rè)應力累積。具有尖端和大曲率等複雜結構的金屬零件(jiàn),在尖端和大曲率位置處存在沉積層形貌尺寸(cùn)偏差,可以通過(guò)製定合(hé)理的掃描(miáo)策略進行控製(zhì);然而,目前切片和路(lù)徑規劃軟(ruǎn)件隻能(néng)進行(háng)簡單的設(shè)計,不能根據零件(jiàn)結構及成形工藝特性進行掃描策略的局部調整。此外,3D打印過(guò)程質(zhì)量(liàng)參數的特征辨識與智能(néng)處理技術還不夠成熟,不能實現成形(xíng)過程工藝參數的自(zì)適應控製。
undefined
3.2 研究方向
1) 成形質量及變形開裂控製。
成形件的內部缺陷及組織特征決定其性能,如何獲得(dé)性能優異,實現內部缺陷、組織性能和工藝條件的(de)一體化控製是大型複雜金屬零件3D打印一個重要研究方向(xiàng)。另外(wài),變形開裂是大型複雜金屬零件3D打印成形(xíng)的(de)常見(jiàn)和致命問題,亟待深入分析不同外形結構(gòu)、熱力環境條件下,金(jīn)屬粉末非平衡(héng)凝(níng)固過程的內應力演化規律,並(bìng)製定相應的預防控製方案。
2) 過程監(jiān)測係統及智能控製(zhì)軟件開發。
大(dà)型複雜金(jīn)屬零件3D打印過程的時(shí)間(jiān)長、路徑複雜多變、不可預見情況較多,導致成形(xíng)質(zhì)量及穩定性較低(dī)。開發3D打印過程的溫度場、外貌尺寸以及變形開裂等問題的實時監測係統,並研製融合分層處理、路徑(jìng)規劃及工藝技(jì)術的自適應功(gōng)能的(de)成形控(kòng)製軟件,對於提高成形質(zhì)量、穩定性和安(ān)全性至(zhì)關重要。
3) 後處理工(gōng)藝技術(shù)開發。
大型(xíng)複雜金屬零件3D打印,由於金屬粉(fěn)末的快速加熱-冷卻以及成形機理、工藝參數複雜,成形零件在尺寸精度、內部缺陷、組織性能等方麵難(nán)以同時達到應用指標;因此,應加強對成形零件的後處理工藝技(jì)術製定和開發研究,提高性能、節約(yuē)資(zī)源、降低成本。
4 結束語
金屬3D打印技(jì)術廣(guǎng)泛(fàn)應用於航空、航天、石化、船舶等工業(yè)裝備領域,具有無(wú)需大型裝(zhuāng)備(bèi)、模具,材料利用率高,製造(zào)周期短(duǎn)、成本低,零件性能優異等突出優點。目前,針對大型複雜金屬零件3D打印技術,國內外已開展了大量的研究工作(zuò),取得了(le)廣泛的應用成果;然(rán)而,分層處理、掃描路徑和策略技術(shù)不成熟,成形過程不穩定,存在變形開裂、內(nèi)部缺陷等(děng)問題,製約了大型複雜金屬零件3D打印技術的工(gōng)程應用。大型複雜金屬零件(jiàn)3D打(dǎ)印技(jì)術還需在(zài)變形開裂和內部(bù)缺陷預防、分層處理和路徑規劃等方麵開展大量研究(jiū)工作。