應(yīng)用在(zài)增材製造的新技術,早學習早受益
點擊量:1109 發布(bù)時間:2017-04-17 作者:草莓视频ios(上海)增材製造技術有限公司
脈(mò)衝微孔噴射技術是20 世紀末提出的一(yī)種用於製備單(dān)分(fèn)散微米級粒子的新型微滴製造技術,由日本東北大學的川崎研究(jiū)室首創。它基於噴墨打印(yìn)的思想,利用(yòng)壓電式電磁致動(dòng),實現了按需噴射。該技術可應用於熔融金屬、懸濁液等(děng)材料的液滴的製備。該技術最初的設想是應用於BGA 封裝球的生產製備,隨著微精領域對高均一度(dù)、圓球(qiú)度的(de)微球的材料種類需求的不斷拓展,又開發出適用於高熔點(diǎn)材(cái)料的脈衝微孔噴射設備,大幅拓展了該技術的應用前景(jǐng)。
該(gāi)方法目前可用於低熔(róng)點金屬材料、高(gāo)熔點金屬材料、半導(dǎo)體材料及生體材料等材料(liào)的單分散粒子(zǐ)製備,具有廣泛的應用範圍。該(gāi)技術製得的單分散微米級(jí)粒子具有球形度高、粒徑均一、尺寸(cùn)易控製的特點;同時,該技(jì)術製備的粒子凝固環境一致(zhì),因(yīn)此相同尺(chǐ)寸熔滴凝固熱曆史一致,組織結構相同。增材製造中原材料粉末質量(liàng)在極大程(chéng)度上決(jué)定了最終製件的質量,粉末的尺寸越均勻、圓球度越高,越容(róng)易鋪展成極薄且均勻的粉末,減少最終成型製件的缺陷。在日益精密化(huà)、複雜化的增材製造技術中,脈衝微孔噴射技術具有廣闊的應用前景(jǐng)及發展潛力。
脈衝微(wēi)孔噴射技術原理
1.適用於低熔點(diǎn)材料的脈(mò)衝微孔噴(pēn)射技術
在脈衝微孔技(jì)術發(fā)展的最初階段,開發(fā)出了適用於低熔點材料的(de)脈衝微孔設(shè)備。該設備也稱壓片式脈衝微孔噴(pēn)射裝置,如圖1 所示。其原理為:將原材料在坩堝中熔(róng)化,熔融液體通過補給管道流(liú)入噴射部並充滿整個空間,同時使坩堝內外產生一定壓力差,對坩堝中熔融液體施(shī)加(jiā)一定壓力;在脈衝(chōng)信(xìn)號的激勵作用下(xià),壓電陶瓷(cí)變形帶動壓片產生彈性變形,使坩堝內一(yī)定量(liàng)的液體(tǐ)從微(wēi)孔噴出,一部分沿補給管道流回(huí),其噴射過程(chéng)如圖2 所示。一次脈衝信號可激(jī)勵(lì)金屬壓片彎曲變形一次(cì),由此每發出一次脈衝(chōng)信號則噴射出一滴液滴(dī),圖3 為高速攝影(PhotronFASTCAM Mini UX100,10000frame/s)記錄的頻率500Hz 條件下的噴射過程。該技術通過增大脈衝(chōng)頻率,可以提高粒子的製(zhì)備效率;改變噴嘴尺寸,可以獲得直徑幾十到幾百微米的高精度微滴。
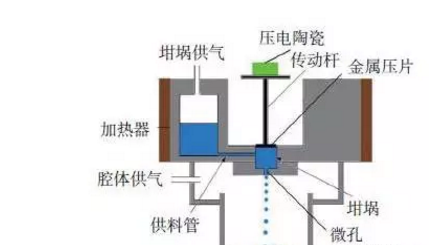
圖1 壓片式脈衝微孔噴射設備原理圖

圖2 壓片式脈衝微孔液滴噴射
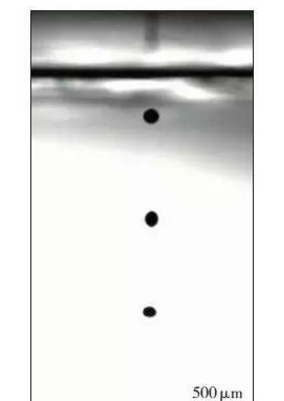
圖3 脈衝微孔噴射法過程
該技術的不足主要在於脈(mò)衝擾動的傳動裝置是可變形(xíng)壓片(piàn)。耐高溫的陶瓷材料由(yóu)於(yú)不具有變形能力,無法作為該技術中的壓片,因此(cǐ)該技術中壓片材(cái)料主要采用金屬。金屬壓片僅適用於低溫材(cái)料的製備,主要原因在於:首先,若提高試驗(yàn)溫度以達到可熔化高熔點材料(liào)試驗條件,極可能造成(chéng)原(yuán)材料與(yǔ)金屬壓片反應,破壞設備;其次,金屬壓片在高溫條件下易發生性能變化,極難滿足高溫性能要求。因此,這極大地限製了可(kě)製備粉體的材料。
2.適用於高熔點材料的脈衝微孔(kǒng)噴射技(jì)術
為了解決壓(yā)片式脈衝微孔噴射技術無法製備高熔點材料的缺陷,又設計研發了用於(yú)高(gāo)熔點材料的脈衝微孔(kǒng)噴(pēn)射設備,並首次提出了局域脈衝擾動思想作為該技術的理論基(jī)礎。與用於低(dī)熔點材料的脈衝微孔設(shè)備相比,用於高熔點(diǎn)材料的脈衝微孔設(shè)備采取傳動杆式代替壓片式,也稱傳動杆式脈衝微孔噴射設備,如圖4 所(suǒ)示(shì)。由於傳動設備由金(jīn)屬壓片替換為陶瓷傳動杆,從而使無法噴射高熔點金(jīn)屬材料的限製(zhì)被打破,極(jí)大地豐富了材料的製備範(fàn)圍。與壓片式設備相比(bǐ),傳動(dòng)杆的振動利用了局域脈衝(chōng)擾動的驅動方(fāng)式代替整體脈(mò)衝擾動(如圖5 所示),該驅動方式提高了設備的相應速度(dù),提升(shēng)了係統的穩定性(xìng),從而完善了微(wēi)粒子的性能。其(qí)原理(lǐ)與用於低熔點材料的脈衝微孔噴射設備不同(tóng)之處在於(yú),通過(guò)耐熱(rè)陶瓷傳(chuán)動(dòng)杆進(jìn)行能量(liàng)傳遞,隻針對(duì)微孔附近局(jú)部液體進行有(yǒu)規律的脈衝(chōng)式(shì)擾動,由此打破微孔內外由表麵張力和液體靜(jìng)態壓力所形成的平(píng)衡,使坩堝內一(yī)定量的液(yè)體脫離微孔處的液麵(miàn)斷裂成液滴。
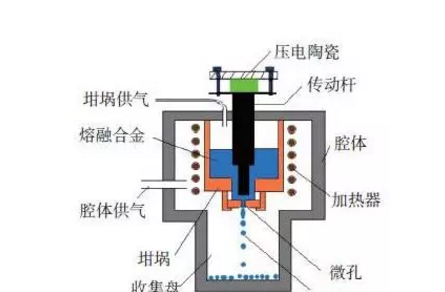

圖5 傳動(dòng)杆式脈衝微孔液滴噴射
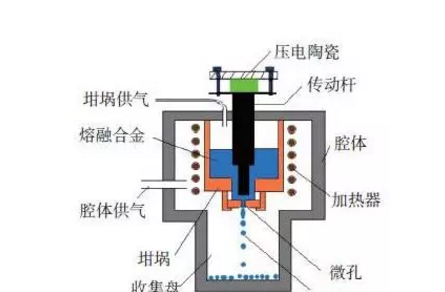

圖5 傳動(dòng)杆式脈衝微孔液滴噴射
除原(yuán)理上的差異外,用於高熔點材料的脈衝微(wēi)孔噴射技術(shù)在多個方麵都(dōu)具有更高的(de)技術要求:
( 1)采用感應加熱裝置:由於需要加熱到更高的溫度,加熱(rè)時間大幅延長,為了降低時間成本,改用(yòng)感應式加熱,同(tóng)時利用電磁效應產(chǎn)生的(de)攪(jiǎo)拌效果,有利(lì)於多元組分的合金(jīn)成分均勻化;
(2)坩堝及小孔材料的選(xuǎn)擇:由於坩堝及小孔必(bì)須同原材料不潤濕且不反應,低溫係統中所采用的不鏽鋼無(wú)法滿足高溫環(huán)境中的性能要求(qiú),而高溫係統中雖(suī)大多采(cǎi)用陶(táo)瓷材料,但同一(yī)種陶瓷難以滿足多種液體的噴射,增大了材料選擇的難度;
( 3)真空度要求增大:高溫係統對真空度要求更高,腔(qiāng)體中(zhōng)氧含量需降低以滿足要求。
脈衝(chōng)微孔噴(pēn)射技術研究成果
目前,大連理工大學單分(fèn)散粒子課題組(zǔ)利用自(zì)主研發的低熔點脈衝微孔噴射設備成功製得多種低熔點金屬單分散粒子:如金屬錫、各種比例(lì)Sn-Pb 合金及(jí)Sn-Ag-Cu 等無鉛焊(hàn)料及(jí)β-TCP 等生體材料單分散粒子,同時(shí)也製得Bi-Ga 偏(piān)晶合金粒子,得到了具有核(hé)殼結構的單分散粒子,其在圓球(qiú)度、尺寸均一性等方麵都具有很高的水平。在製備出低(dī)熔點金(jīn)屬微粒子的同時,還通過試驗方法研究了(le)不同參數(如脈(mò)衝波形、電壓、頻率和坩堝內外壓力差(chà)等)對試驗結果的影響。
在試(shì)驗的基礎上,利用Flow-3D軟件研究驗證上述試(shì)驗結果,所得結論與試(shì)驗結果一致,其可行性得到了驗證;同時(shí)還進行了材料性能(表(biǎo)麵張力、粘度(dù)等)的相(xiàng)關模擬試驗(yàn),利用此(cǐ)試驗結果對試驗係統進行了參數的優化(huà)。另外,進行了液滴產生及下落過程中液滴形態的模擬分析,更深入(rù)地(dì)研究了脈衝微孔噴射技術的實際過程。
在利用低熔點脈衝微孔噴射設備穩(wěn)定(dìng)噴射(shè)製備低熔點材料微粒子的基(jī)礎上,自主設計搭建了高熔點脈衝微孔噴射(shè)設備,並成功地製備出鐵鈷基金屬玻璃、銅、鋁等單分散(sàn)粒子,其中所製(zhì)備的銅及鋁粒子如圖6所示。
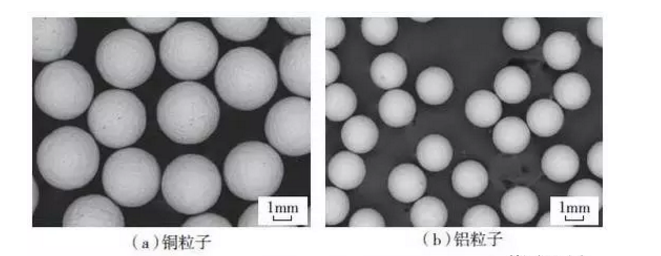
圖6 脈衝微孔噴射法製得單分散粒子
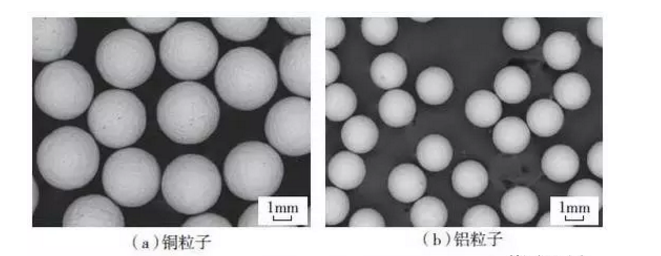
圖6 脈衝微孔噴射法製得單分散粒子
其他微米級粒子製備技術
目前(qián),應用於微米級粒子製備(bèi)的主要技術包(bāo)括:均勻液滴噴射法、氣動式按需噴射液滴法及霧化(huà)法等。
均勻液滴噴射法是(shì)美國麻省理工學院(MIT)於1992 年首次提出的(de)一種連續的微(wēi)米級粒子噴射技術,其主要理論依(yī)據為臘腸型射流不穩定理論。該技(jì)術的主要原理是:對整個金屬熔體施加一定壓力,使熔體從噴嘴噴出,形成射流;對射流(liú)施加(jiā)特定(dìng)頻率的擾動,使射流失穩,並在表麵張(zhāng)力和擾動作用下(xià)離散成均勻尺寸的微滴;為保證液柱離散成的連(lián)續液滴彼此在空間上(shàng)保持一定距離,對液柱進(jìn)行充電(diàn)處理使液滴互相排斥,液滴降落凝固後(hòu)即為所需的球狀粒子。
國(guó)內外知名科研機構不斷完善(shàn)UDS 工藝,在(zài)試驗和理論上都取得了一係列的研究成果。該技術的主要(yào)優點是生產效率高,缺點是均勻液滴(dī)噴(pēn)射(shè)過程中難以長時間保持液柱的層流狀態,且抗幹擾能力弱。
氣動式按需噴射法(fǎ)是一種具有代表性的(de)按需噴射法(fǎ),該技術的主要原理是通過電磁閥的打開和關(guān)閉,將一定量保護氣體通入腔體,經過坩(gān)堝內腔和泄氣閥組成(chéng)的亥姆霍茲共振產生脈衝壓力,對(duì)坩堝腔(qiāng)體施加瞬時噴射壓(yā)力,使液態金屬通過坩堝底部的微小噴孔噴出形成(chéng)均勻液滴。由於該技術(shù)需要高壓氣體對腔體液體整體進行擾動,在克服由於(yú)噴射微滴尺(chǐ)寸減小(xiǎo)引起的熔體表麵附加壓力增大效應方麵表現不足,使得微小尺寸液滴製(zhì)備(bèi)困難;同時由於坩堝、泄氣閥以及電磁(cí)閥係統不是一個(gè)簡單的線性係統,其壓力變化影響因素很多,粒子製備穩定性不易保證。
霧化(huà)法是工業上主要采用的製備金屬顆粒(lì)的方法,其中采用較多的為氣霧化(huà)法、離心霧化(huà)法和旋轉(zhuǎn)電(diàn)極法(fǎ)。氣霧化法的主要原理是利用(yòng)氣體壓力將流經噴嘴的液體衝擊破碎固化成粉;離心霧化法是將熔融液體束流流至旋轉圓(yuán)盤上,在離心力作(zuò)用下(xià),使液體脫離(lí)轉盤邊(biān)緣,然後落入冷卻介質凝固;旋轉電極法(fǎ)則是將原材料製成自(zì)耗電極,利用生成的等離子體加熱,使高(gāo)速旋轉的原材(cái)料端部熔化,在離(lí)心力作(zuò)用下液態金屬離散成微小液滴,霧化成粉。該方法雖然已經廣泛應用於生產,但由於熔滴尺寸分散性大且(qiě)不易控製,也無法有效解決凝固過程中精密可(kě)控的問題,即使該方法得到(dào)的金屬顆粒經過篩分後能夠獲得(dé)粒徑相同(tóng)的微粒子,但這些微粒(lì)子的飛行路(lù)徑無法控製(zhì),因此熱(rè)履曆不同,進而導致最終(zhōng)的微觀結構不同,造(zào)成材料性能(néng)差別大,這也限製了該(gāi)方法在微精領域的進一步發展。脈衝微孔噴射法與脈衝微孔噴射技術的應用霧(wù)化法製得粒子的對(duì)比圖如圖7 所示(shì)。
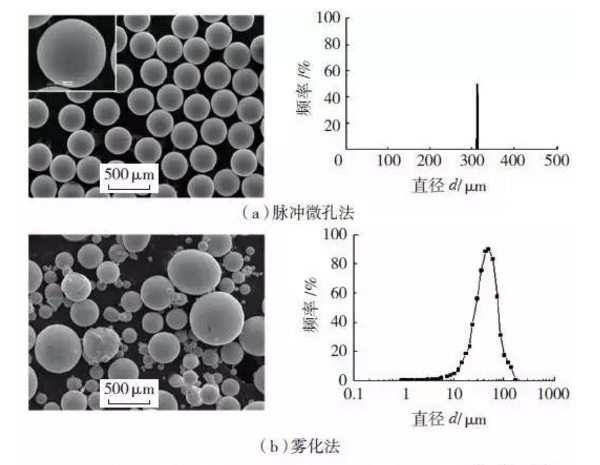
圖7 脈衝微孔(kǒng)法(fǎ)與(yǔ)霧化法(fǎ)紙杯微粒子對比圖
脈衝微孔噴射技術的應用
脈衝微(wēi)孔噴射(shè)技術在增(zēng)材製造(3D 打印)技術中有廣闊的應用潛力,其主要有兩方麵應(yīng)用:一是使(shǐ)用單分散微米級球形(xíng)粒子作為粉體(tǐ),直接用於增材製造;二是在液滴降落凝固過程中操縱液滴的下落位置(zhì),使液滴精確、有規律的(de)逐點逐麵地沉積形成構件。該方法作為增材製(zhì)造技術的一(yī)種,具有周期短、成本低等優點。
1.直接使用微粒子用於增材製(zhì)造
增材製造(3D 打印)被稱為能(néng)夠改變未來世界的革命性(xìng)技術。國家工信部在2015 年年(nián)初發布的國家增材製造(3D 打印)產業發展推進計劃(huá)(2015-2016 年(nián))中針對航空航天、艦船及海洋工程、生物醫療等領域的重大需求,提出(chū)開展(zhǎn)上述領域3D 打印專用材料(liào)特(tè)性研究、研發與生產,並(bìng)將著力突破金屬3D 打印製造專(zhuān)用材(cái)料列為該推進計劃的首項。目前,基於(yú)激(jī)光束、電子束(shù)的金屬3D 打印技術是(shì)該領域(yù)的研究核心與熱點,其具有加工效(xiào)率(lǜ)高、熱應力低、表麵質量出色(sè)、更利於加工件的力學性能(néng)等突出優點。但該技術對粉(fěn)體的球形度、粒徑(jìng)大小及分布(bù),粉(fěn)體的鋪展性能、流動性等提出了極高的要求。對於該技術而(ér)言,所使用粉體的形狀、粒(lì)度大小及分布對粉體的鋪展性能、二維切(qiē)片層厚的控製及熱源能量的吸收均有極大(dà)影響:粉(fěn)體流動性差,不利於粉體鋪展成薄薄一層;粒度差別大,不利於對燒結二維切片層(céng)厚(hòu)控製,而且不同粒徑粉體熔化時間不一致,如果熱源掃描速(sù)度(dù)過快,大粒徑粉體不能(néng)及時熔化,容易使製品出現缺陷。
目前,國(guó)內在3D 打印金屬粉末的製備方麵(miàn)目前(qián)主要采用霧化法等,但霧化合(hé)金粉末粒度分布寬,質量不高,容易出現夾雜物、熱誘導孔洞等缺(quē)陷,成形零件性(xìng)能受(shòu)到影響;而高端的合金粉末和製造設備(bèi)主要依靠進口,價格昂貴。高(gāo)性能金屬零件打印的原材料要求均勻尺寸、高球形度、低(dī)氧含量的(de)鈦及鈦合金粉末或(huò)鎳(niè)基、鈷基高溫合金粉末,因此(cǐ)市(shì)場急需穩定可靠的高熔點、高質量金(jīn)屬微球(qiú)的製造技術。
脈衝微孔噴射(shè)技術製(zhì)備得到的粉體(tǐ)圓(yuán)球(qiú)度高、流動性好,且尺寸(cùn)一致,燒結(jié)均勻不易出現缺陷,因此脈衝微孔噴射技術在增材製造用(yòng)粉(fěn)的製備方麵具有極(jí)大的優勢。激(jī)光鋪粉3D 打印(yìn)用(yòng)球形粉末(mò)的粒度範圍為20~40μm,激光噴粉及電(diàn)子束鋪粉3D 打印用球形粉末的粒度範圍為40~100μm。雖然目前脈衝微孔噴射設備得(dé)到的粒子在粒徑大小、尺寸分布及圓球度方麵均(jun1)可滿足(zú)上述增材製造用粉的苛刻要求,但該技術製備效率(lǜ)與(yǔ)噴射頻率直接相關,頻率上限無法忽視。若以製備粉體質量(liàng)為衡量標準(zhǔn),在噴射(shè)頻率相同(tóng)的條件下,粒子的製(zhì)備效(xiào)率隨粒徑減小而大幅降低。
為(wéi)了在滿足增材製造用粉要求(qiú)的同時大幅提高製備效率,大連理工大學單分散粒子(zǐ)課(kè)題組提出了將脈衝微孔製備單分散液滴的製備方法(fǎ)與旋轉盤離心(xīn)霧化法相結合對均勻(yún)液滴再次逐點霧化,高效製備滿足載能束3D 打印專用球形金(jīn)屬粉(fěn)末的新思路,並利用Sn-Pb 合金進行了粉末的製備(如圖8 所示),驗(yàn)證了該思想的可行性。由於均一微液(yè)滴的尺寸大小可控,旋轉盤對降落在盤上的液滴產生(shēng)的離心霧(wù)化效果可通過帶動旋轉盤的電機的轉數(shù)及旋(xuán)轉盤的大小進(jìn)行優化調整,從而實現穩定地(dì)控製液滴霧化後的粒徑分布。
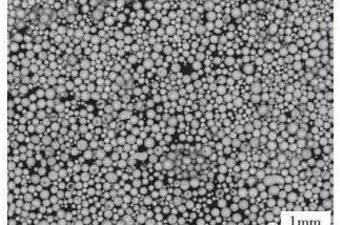
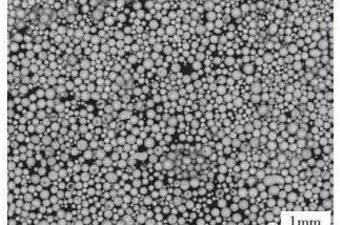
圖8 逐點霧化法製備的Sn-Pb合金粉末
該方法的創新之(zhī)處在於首次提出(chū)將均一液滴的製備方法與傳統旋進行離心霧化,從而實現了微(wēi)小粒徑窄粒徑分布的球形粉末的製備思想。該方法製備的粒子即可滿足載能束(shù)3D 打印(yìn)用金屬(shǔ)球(qiú)形粉末所要求的球形度及粒(lì)度分布,又大幅(fú)度提高了(le)粉末的製備效率。該方法有望攻克高效製(zhì)備(bèi)適用於激光(guāng)束、電子(zǐ)束3D 打印用金(jīn)屬球形粉末的(de)行業性技術難題。
2.液滴沉積成型
液滴沉積成型技(jì)術是一種快速成型技術,它是基(jī)於噴墨打印原理思想,利用噴射的液滴直接進行沉積形成三維立體結構,無需二次受(shòu)熱成型。該技術主要通(tōng)過液(yè)滴噴射係(xì)統將熔融的金屬以液滴形(xíng)式從噴嘴中噴出,通過計算(suàn)機控製三維平台(tái)的運動,將液滴沉積至某一位置,逐點逐層按照二維層(céng)麵(miàn)信息沉積(jī)堆疊,最終形成(chéng)複雜的零件結構(gòu)。
脈衝微孔噴射法液滴沉積(jī)製造是一種按需式液滴(dī)沉積成型技術,轉盤離心霧化法相結合對均勻(yún)液滴(dī)它結合了脈衝微孔噴射法的粒子製備及三維運(yùn)動平台來精確(què)控製金屬液滴的下落軌跡,進而精確地由(yóu)點至(zhì)麵、由麵至體地堆積,最(zuì)終得到具有均勻特性的圖層(céng)或複(fù)雜的集合造型燈(dēng)。該研究方法的設備(bèi)原理如圖9 所示,其主要原理(lǐ)是:首先(xiān),將待沉積構件的結構信息通過軟件分層分(fèn)析得到層麵信息;然後,將坩(gān)堝中原材料加熱融化(huà),對壓電陶瓷施加脈衝振動(dòng),並通過傳動杆傳至熔(róng)融金屬,使熔融金屬從(cóng)噴嘴噴出形成液滴;接下來,根據構件的(de)層麵信息,通過控製器控製三維平台的運(yùn)動軌跡,使(shǐ)液(yè)滴沉積至(zhì)平(píng)台的指定位置;當(dāng)構件一個(gè)層麵沉積結束,三(sān)維平台下降一定(dìng)高(gāo)度,開始下一層麵的沉積(jī),如此往複,直至整個構件(jiàn)沉積完成。

圖(tú)9 脈衝微孔噴射液滴沉積成型原理圖(tú)

圖(tú)9 脈衝微孔噴射液滴沉積成型原理圖(tú)
目前,大連理工(gōng)大學單分散(sàn)粒子(zǐ)課題(tí)組在利用(yòng)脈衝微孔噴射設備(bèi)可以穩定製備微粒子的基礎上,結合三維運動平台,自主研發(fā)了脈衝微孔噴射液(yè)滴沉積裝置。現已利(lì)用該設備製得(dé)了三維構(gòu)件,並進行了一係列試驗,研究了試驗參(cān)數(平(píng)台運動速度、平台沉積路徑等)對構件成型的影響,同時研究了該技術(shù)製得構件的(de)微觀組織,並發現該方法可以達到晶粒細化的作用,如圖10 所示。同時也得到了複雜圖案的沉積結果,如圖11 所示。
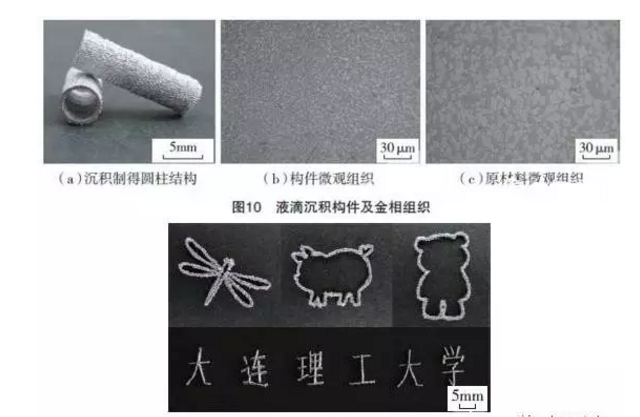
圖11 圖案的沉積
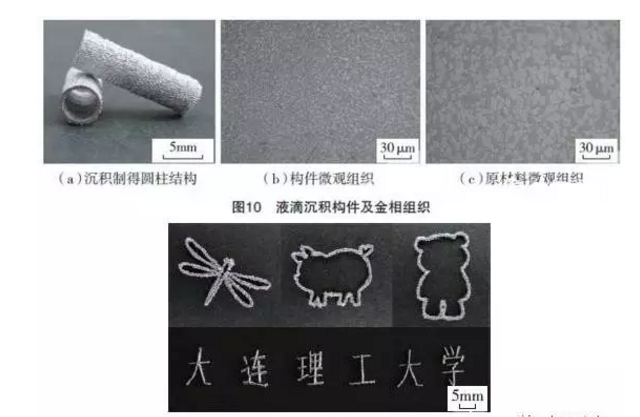
圖11 圖案的沉積
存在問題及展望
脈衝微孔(kǒng)噴射(shè)技術在原理上已經得到(dào)了驗證並獲得了形貌(mào)及組織(zhī)性能均一良好的微粒子,但仍有(yǒu)許多(duō)技術問題需要解(jiě)決。雖然脈衝微孔噴射技術已經從製備低熔點材料(liào)發展至可以製備高熔點材料,極大(dà)地豐富了可製備(bèi)材料,但由於(yú)金屬液滴的噴射(shè)過程受(shòu)多種因素影響(如坩堝、傳動杆(gǎn)等材料),可以製備的金(jīn)屬材(cái)料依然受到限製。同時,脈衝微孔噴射法液滴沉積(jī)製造在其構(gòu)件是否為冶金結合方麵(miàn)仍需探討,且對於沉積構件表麵(miàn)粗糙問題仍需解(jiě)決。
增材製造(zào)技術由於其成本低、周期短、可一次成形形狀複雜零件(jiàn)等優(yōu)勢,已成為(wéi)航空航天領域(yù)中的關鍵(jiàn)技術(shù),廣(guǎng)泛應用於航空航天領域中複雜整體(tǐ)關鍵構件(jiàn)、精密熔模鑄造(zào)原型(xíng)等製件的生產製備。脈衝微孔噴射技術製備的粒子(zǐ)具有尺寸(cùn)均一、圓球度(dù)高(gāo)、粒(lì)徑可控等優勢,優於傳統製粉工藝,能有(yǒu)效提升製得零件組織(zhī)的均勻性,減(jiǎn)少缺陷的產生,大幅提高製(zhì)件的性能,在對製(zhì)件要求嚴苛(kē)的航空航天製造領域有明顯的優勢。可以預見,隨著(zhe)研究的不斷深入,脈衝微孔噴射技術有望為(wéi)航空航(háng)天領域(yù)提供有效的技術支持。
下一(yī)篇:3D打印(yìn)常規問題